This is what LABPLAS, a rapidly growing SME from Sainte-Julie, has grasped

By Emmanuelle Gril, le Journal de Montréal
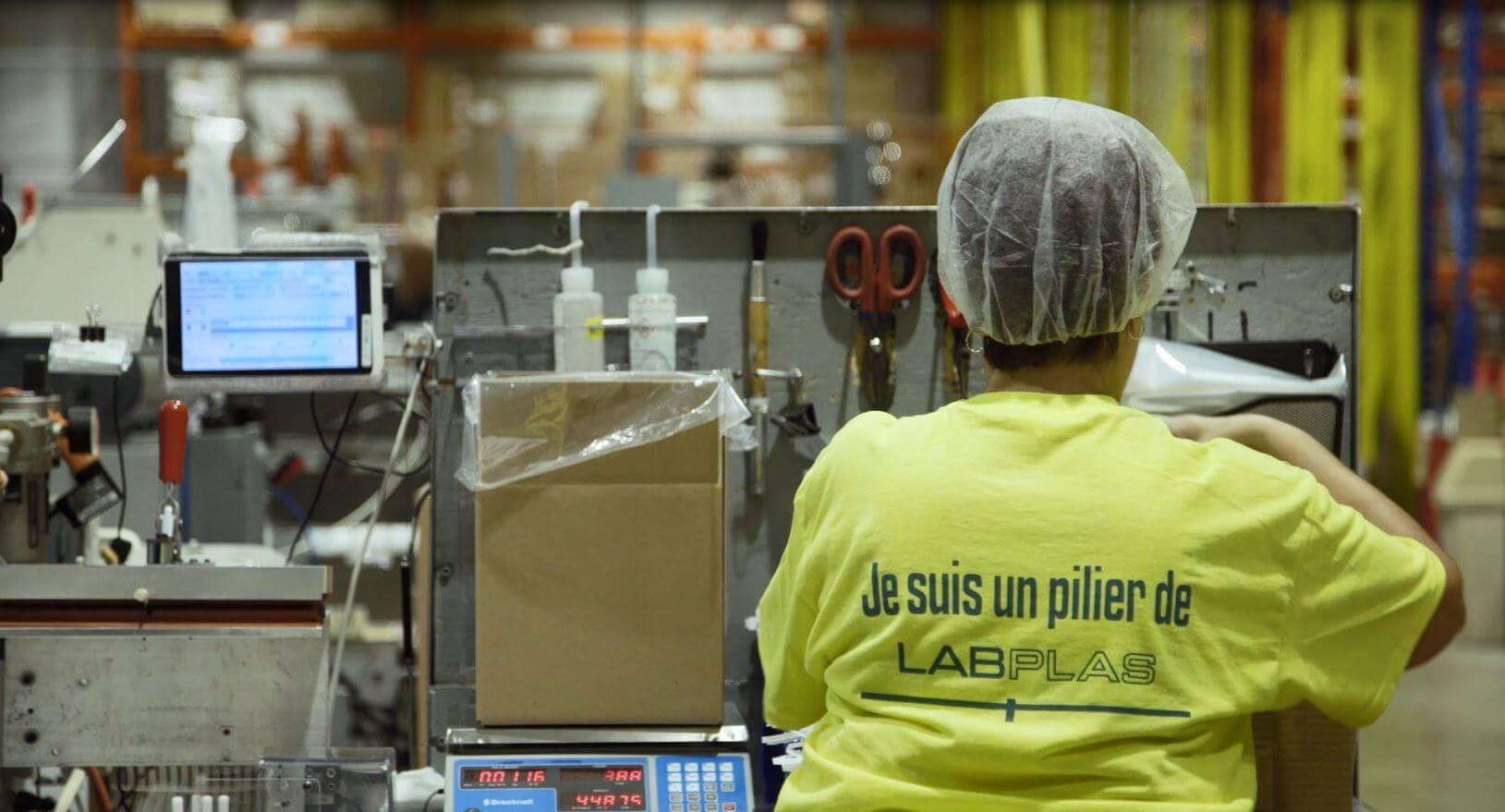
Founded in 1987, LABPLAS embarked on its digital transformation as early as 1994. Today, its factory is almost fully connected, and technological changes have generated significant added value.
In the pharmaceutical, agri-food, environmental research, and veterinary sciences industries, LABPLAS operates and provides sterile sampling solutions for analysis purposes. The products of this Sainte-Julie-based company are sold in over 50 countries through a network of 175 distributors. This growth is not only based on its expertise and know-how but also on data utilization.
Factory 4.0
It all began with the implementation of an initial resource management system, followed by a customer relationship management software. Subsequently, software solutions were developed to automate data collection related to quality management, industrial process management, and inventory management.
“But it’s all well and good to be a ‘datavore,’ you still need to know what to do with all this information and extract value from it!” says General Manager Benoît Brouillette. At LABPLAS, they were able to generate reports automatically, identify where time losses were occurring, and ultimately improve production.
“For example, we were able to identify which types of stops occurred most frequently and on which machines. Once that was done, we installed a robot, which solved the problem. We then equipped all 20 of our production lines in the same way, and the return on this investment took only a few months,” he illustrates.
Making Better Decisions
With all production machines connected, LABPLAS has truly become a Factory 4.0. Out of the company’s 100 employees, 15 are dedicated entirely to digital needs. “We value data not only to help improve management and processes but also behaviors on the production floor. The beauty of data is that they allow us to support all our decisions with numbers and performance indicators,” highlights the General Manager.
This also contributes to reducing unnecessary transportation. “For example, based on order reports, at the beginning of each month, we move all the product pallets located on the upper floors to the first floor of the warehouse, which will need to be delivered in the current month. This way, we avoid unnecessary movements and maximize the shipping process,” details Benoît Brouillette.
Other projects are also on their radar, including real-time monitoring of the organization’s activities. “The 4.0 transition never has an end because technology is constantly improving. We continue to grow and pursue the valorization of all the data we have,” he concludes.
Leave A Comment
You must be logged in to post a comment.